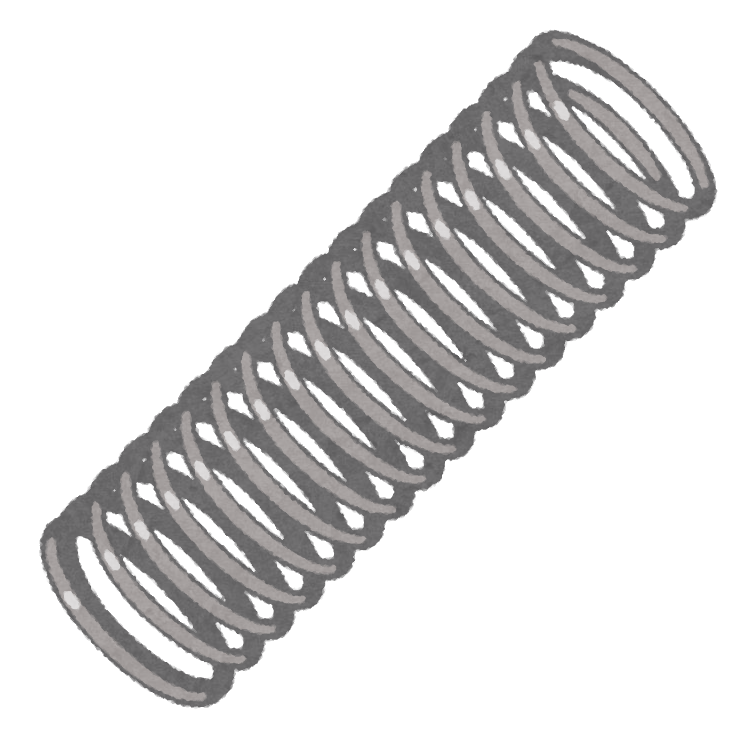
2025.07.16
ばね全般スマートフォンのボタン、自動車のサスペンション、時計のぜんまい……これらに共通するのは「板ばね」という技術です。
「複雑な形状の隙間に、円筒形のコイルばねが入らない…」
「部品コストを30%削減しながら、性能も向上させたい…」
「軽量化が求められるが、強度は妥協できない…」
このような設計課題を抱えている方にとって、板ばねは革新的な解決策となる可能性があります。
板ばねは単なる「平たいばね」ではありません。
曲げ変形の弾性力を巧みに活用することで、コイルばねでは実現できない複雑な形状設計を可能にし、製造コストを大幅に削減できる優れた技術です。
本記事では、6種類の板ばねの構造特性から材質選定の実践的なポイントまで、設計者が知っておくべき知識を体系的に解説します。
きっと「こんな使い方があったのか!」という新たな発見があるはずです。
板ばねとは?
板ばねはおもに金属板を使用したばね部品で、曲げ変形の弾性力を活用してさまざまな機能を提供します。
ここでは板ばねの基本的な定義と特徴、そして他のばね種類との構造的な違いについて解説していきます。
板ばねの定義と特徴
板ばねの多くは金属板を加工して作られており、力が加わるとたわんでエネルギーを蓄え、力が解放されると元の形状に戻る弾性特性を持っています。
ばね用の特殊鋼やステンレス鋼を材料とし、打抜加工や曲げ加工によって製造されるのが一般的です。
また、板厚1mm程度以下のものを一般的に「薄板ばね」と呼び、形状に明確な決まりはなく用途に応じて自由な設計が可能な点が大きな特徴となっています。
このため、「押さえる」「挟む」「固定する」「復帰させる」といった幅広い機能で活用されており、製造コストも比較的安価に抑えられることが多いです。
コイルばねや線ばねとの違い
コイルばねが線材を螺旋状に巻いた立体構造であるのに対し、板ばねは平面的な板状の形状が基本となっています。
コイルばねは主に圧縮や引張の軸方向の力に対応しますが、板ばねは曲げ変形による弾性力を利用するため、より複雑な形状設計が可能です。
また、線ばねには圧縮コイルばねやねじりばねなどがありますが、これらは専用のコイリングマシンで製造されるのに対し、板ばねはプレス加工やマルチフォーミング加工で製造します。
このため板ばねは設計自由度が高く、限られたスペースでも効率的な配置ができ、部品との一体化や複合機能の実現も容易になっています。
板ばねの代表的な種類と構造
板ばねは形状や構造によっていくつかの種類に分類され、それぞれ特有の特性と用途を持っています。
ここからは、各種類の構造的特徴と設計における基本的な考え方について詳しく解説します。
重ね板ばね
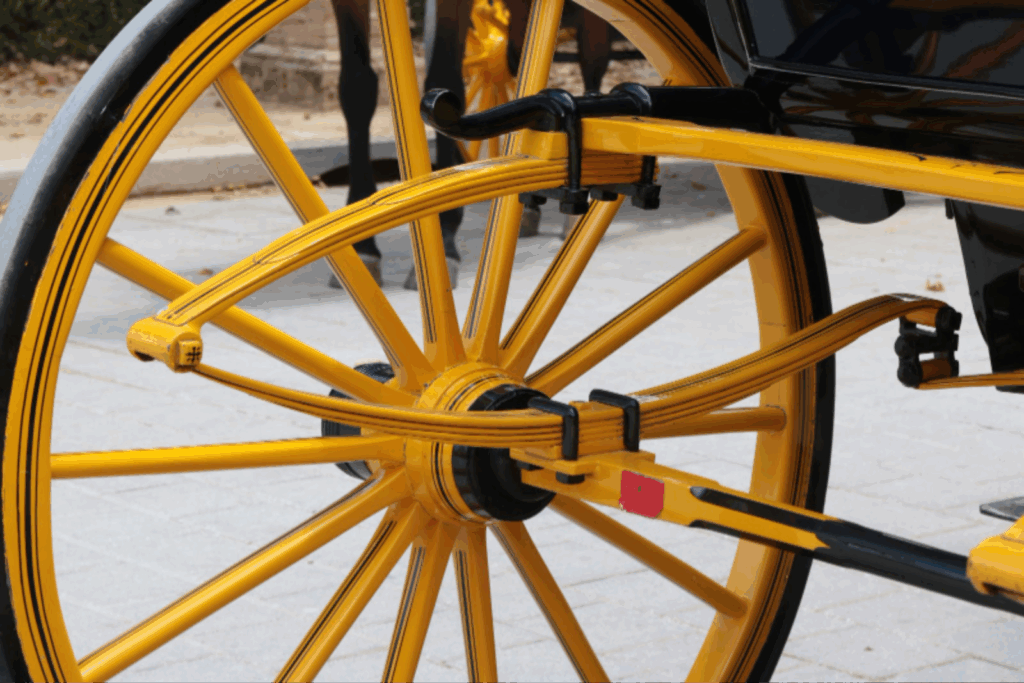
重ね板ばねは、長さの異なる複数枚の板状ばねを重ね合わせて作られる構造が特徴です。
複数枚を重ねることで使用時の応力が各板に分散され、単板では得られない高い耐久性と荷重能力を実現しています。
板材同士が接触・摩擦することで振動減衰効果も発揮し、この特性を活かしてトラックや貨車のサスペンションに広く採用。
現場では「リーフスプリング」とも呼ばれ、重量物を運搬する車両において路面からの衝撃を効果的に吸収する役割を担っています。
構造がシンプルで製造コストも抑えられるため、大型車両の足回りには欠かせない重要な部品です。
薄板ばね
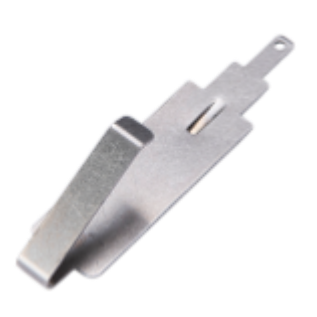
薄板ばねは一般的に板厚1mm以下の薄い金属板を加工したばねで、「板ばね」として最も広く使用されている種類です。
平板やフープ材に打抜加工、曲げ加工、潰し加工などを施すことで製造され、形状に明確な決まりがないため設計自由度が極めて高い点が特徴。
電池ケースの電極、文具のクリップ、スイッチ部品、抜け止め金具など身近な製品から精密機器まで幅広い用途で活用されています。
また組立作業者にとって取り扱いが容易で、エネルギー吸収能力も高く、製造加工の自由度も高いんです。そのため、現代の機械設計において最も汎用性の高いばね部品として欠かせない存在となっています。
皿ばね
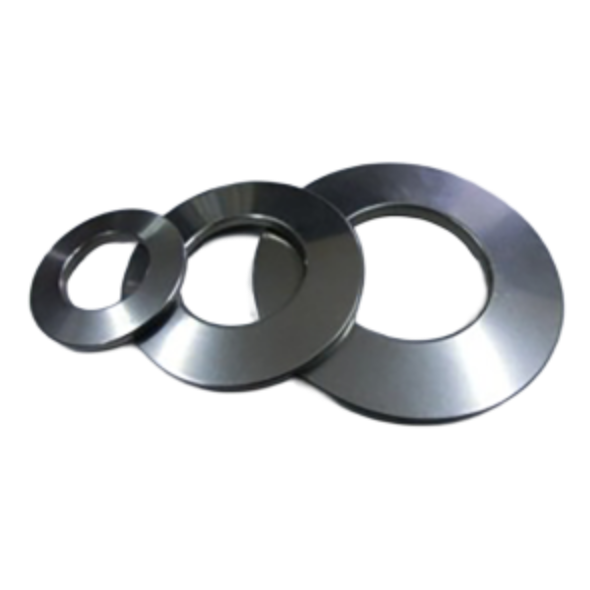
皿ばねは、中心に穴が開いた円盤状の金属板を円錐形に成形したばねで、底のない皿のような独特な形状をしています。
小さな取付スペースで大きな荷重を受けられて、コイルばねが設置できないような狭い場所でも使用可能な点が最大の特徴です。複数枚を並列や直列に組み合わせることで様々なばね特性を得られ、並列重ねでは荷重容量が増加し、直列組み合わせではたわみ量が拡大します。
自動車のクラッチやねじの緩み止め座金、建築物の防震装置など幅広い分野で活用。特に限られたスペースで、高い荷重能力が求められる用途において威力を発揮しています。
渦巻きばね
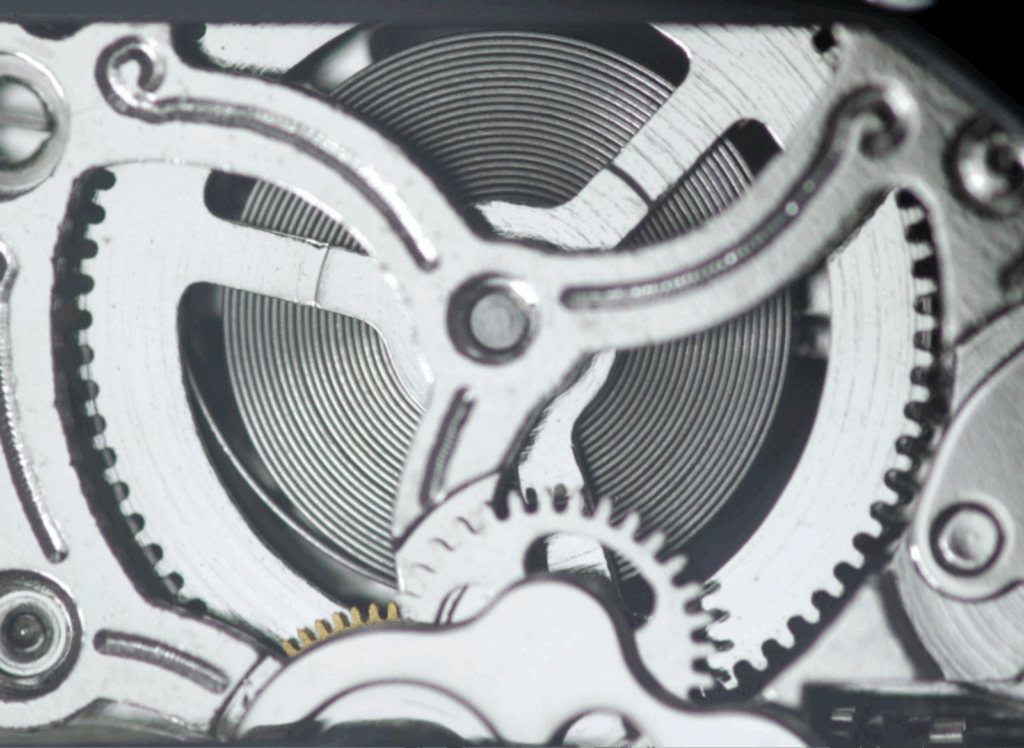
渦巻きばねは、薄い帯状の金属材料を平面内で渦巻状に巻いたばねで、「ぜんまいばね」とも呼ばれています。
接触型と非接触型の2種類があり、接触型は隣接するコイル同士が接触して摩擦による減衰効果を持つ一方、非接触型はコイル間に隙間があり復元力が均一という特性があります。
一端を引っ張ることで弾性エネルギーを蓄積し、解放時に回転力として動力を発生させる仕組みなんですね。
機械式時計のぜんまいや自動車のシートベルト巻取り装置、シートリクライニング機構などに使用され、長時間にわたって安定した動力を供給できます。
この特性から、精密機器や省エネルギー機器において重要な役割を果たしています。
竹の子ばね
竹の子ばねは、長方形断面の板材を円錐状(テーパー状)に巻いて作られるばねで、竹の子のような見た目をしています。
板材を螺旋状に巻いて円錐形を形成し、連続したテーパー形状が特徴です。
荷重がかかると非線形な変形特性を示し、最初は柔らかく変形し、ある荷重域で剛性が急増する2段階の荷重特性を持ちます。この独特の荷重特性により、省スペースで大荷重・高エネルギー吸収が必要な用途に適しており、主に産業機械や自動車部品のクラッチ・サスペンション等で使用されています。
一部では明確な操作感を求めるスイッチ用途にも採用され、特殊な荷重特性が求められる場面で重要な役割を果たしています。
ファスナばね
ファスナばねは、ばねの弾性を利用した締結部品の総称で、薄板ばね型のクリップ状のものから、ばね座金、止め輪、スプリングピンなど多様な形状があります。
弾性変形により相手部品を固定する仕組みを基本とし、多くの種類では工具を使わずに手作業で取り付けや取り外しができる利便性があるのが特徴です。
代表的な特徴として、作業効率の向上とメンテナンス性の良さが挙げられ、自動車の内装部品や電子機器の筐体固定などで広く活用。
作業効率と確実な固定を両立させる必要がある製造現場において、組み立て作業の効率化に大きく貢献する重要な機能部品として位置づけられています。
応力のかかり方と形状設計の基本
板ばねの設計において最も重要なのは、限られた容積内で必要なばね荷重やたわみを得るための形状選定と、ばねに生じる最大応力の位置と大きさの推定です。
板ばねは主に曲げ変形による応力が発生し、固定端で最大となる傾向があります。
応力は「力÷断面積」で表され、材料に生じる応力が弾性限界を超えると永久変形や破損が生じるため、許容応力内での設計が必須です。形状設計では板厚、板幅、長さの関係性が重要で、たわみ量は長さの3乗に比例し板厚の3乗に反比例するという基本特性を理解する必要があります。
また、切り欠きや穴がある部分では応力集中が発生するため、実際の設計では計算値に安全率を考慮し、試作による検証を行うことが重要です。
使用される材質とその選定理由
板ばねの性能は材質選定によって大きく左右されるため、使用環境や要求仕様に応じた適切な材料選択が重要です。ここでは、代表的な材質の特徴と選定理由について詳しく解説します。
ステンレス鋼
ステンレス鋼は板ばね材料として最も広く使用される材質で、特に耐食性と熱に対する安定性が高く評価されています。
ばね用ステンレス鋼帯として、SUS304-CSPやSUS301-CSPが主に使用され、ばね特性の強度によって1/2H、3/4H、Hの3段階に分類できます。
SUS304-CSPは汎用性が高く、錆びに強いという特性から幅広い用途で採用されており、SUS301-CSPはより高いばね特性が要求される場合に選択されます。
板厚0.5mm以下では少量製作でも精度の高い板ばねを製作することが可能で、電子機器、精密機器、医療機器など清潔性が求められる分野において重要な材質です。
リン青銅
リン青銅は優れた電気伝導性と耐食性を兼ね備えた銅系合金で、電気機器や電子部品の接点材料として重要な役割を果たしています。
ばね用リン青銅として、主にC5191やC5210が規格化されており、銅と錫の合金にリンを少量添加することでばね特性が向上しています。
鋼材と比較して弾性係数が小さいため、同じ形状でもばね定数を小さくでき、柔らかなばね特性が得られることが特徴です。
電池ケースの接点、コネクタ、スイッチ部品、通信機器など通電性が重要な用途で多用されており、非磁性であることも電子機器における重要な選定理由となっています。
ハイテン材
ハイテン材(高張力鋼板)は、通常の鋼材よりも高い引張強度を持つ材料で、多くの場合340MPaから790MPaの引張強度を有し、490MPa以上のものが一般的です。
最大の特徴は比強度の高さで、製品を薄肉化しても必要な強度を確保できるため、大幅な軽量化が実現できます。
自動車業界では燃費向上のため車体軽量化が急務となっており、モノコック構造の車体にハイテン材を使用することで、重量削減と同時に高い安全性を確保しています。
ただし、強度が高いゆえに成形性や溶接性に課題があり、金型の強度や精密な加工技術が要求されるため、高度な製造技術を持つメーカーでの加工が必要です。
樹脂
樹脂材料は、金属では実現できない特性を求める場合に選択される材質で、軽量性、絶縁性、耐食性などの優れた特徴を持っています。
プラスチックは金属と比べて「軽い」「錆びない」「加工が容易」な点がメリットですが、強度が低いことが難点です。この強度不足を補うため、繊維強化プラスチック(FRP)・ガラス繊維強化プラスチック(GFRP)・炭素繊維強化プラスチック(CFRP)などの複合材料が開発されています。
電子機器の筐体部品や自動車内装部品、医療機器など軽量化と絶縁性が重要な用途で採用。成形自由度の高さから複雑な形状の一体成形も可能です。量産性とコスト面でも優位性があり、大量生産製品において重要な選択肢となっています。
耐久性・耐熱性・コスト面での特徴
材質選定における重要な判断基準として、耐久性・耐熱性・コストの3つの要素が挙げられます。
耐久性ではステンレス鋼とハイテン材が優秀で、繰り返し荷重に対する疲労特性や腐食環境での長期使用に適しています。耐熱性については実験データに基づく目安温度があり、使用環境が酸性・アルカリ性かなどの腐食環境も大きく影響。
インコネルやハステロイなどの特殊合金は、400℃以上の高温環境でも使用可能ですが、コストが大幅に上昇します。コスト面では炭素鋼系が最も経済的で、ステンレス鋼、銅系合金、特殊合金の順で高くなります。
樹脂材料は材料費は安価ですが、金型費用が必要なため量産での使用が前提となるでしょう。最適な材質選定には、使用環境や要求性能、製造数量を総合的に考慮した判断が不可欠です。
まとめ
板ばねは、従来の固定方法や機械的な仕組みに代わる革新的な解決策です。
ネジ締めやロウ付けなどの従来工法からワンタッチ着脱への変革、複雑な機械構造をシンプルな弾性機構に置き換えることで、作業効率の向上とメンテナンス性の改善を実現できます。
適切な種類と材質の組み合わせにより、従来工法では困難だった課題を解決する板ばねの選定が可能となるでしょう。
設計自由度の高さと製造コストの優位性を活かし、次世代の製品開発にぜひお役立てください。
関連ブログ
-
皆さんご存じの通り、ばねは英語でスプリング(Spring)とよびます。このスプリ...
-
「金属ばね製造技能士」とは
ばね製造会社で働く者にとっては、とても重要な資格「金属ばね製造技能士」についてご... -
板ばねってどう作るの?~マルチフォーミングの場合~
板ばねの「マルチフォーミング加工」に焦点を当て、詳しくご紹介します。...