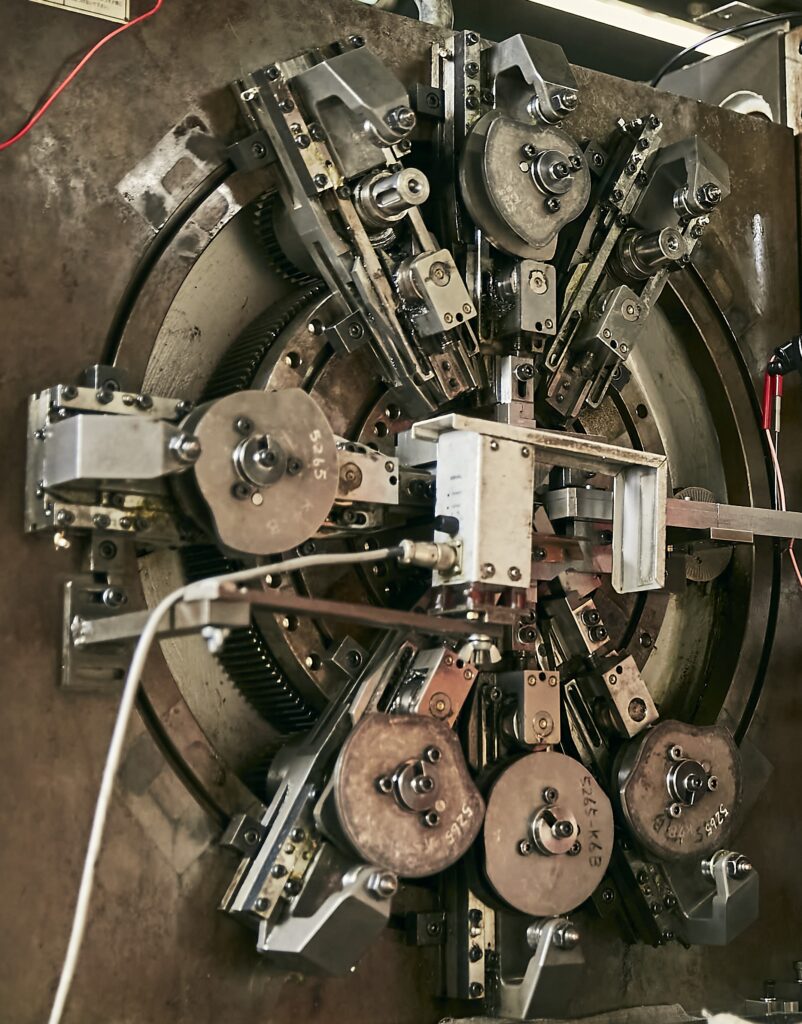
2025.07.22
光洋のばね(最終更新日:2025年7月22日)
クイックファスナーは流体を流す配管同士の接続部分を固定する留め具として使われる部品(薄板ばねの一種)です。今回は、製造に使う各部品の図面を全て作りきるところから、トラブルポイントの検討までの流れについてお伝えします。
本シリーズは第3弾となります。ぜひ第1~5弾もご覧ください!
【目次】
クイックファスナー曲げ工程
曲げ越し量
カムタイミングの設定
トラブルポイントの検討
クイックファスナー曲げ工程
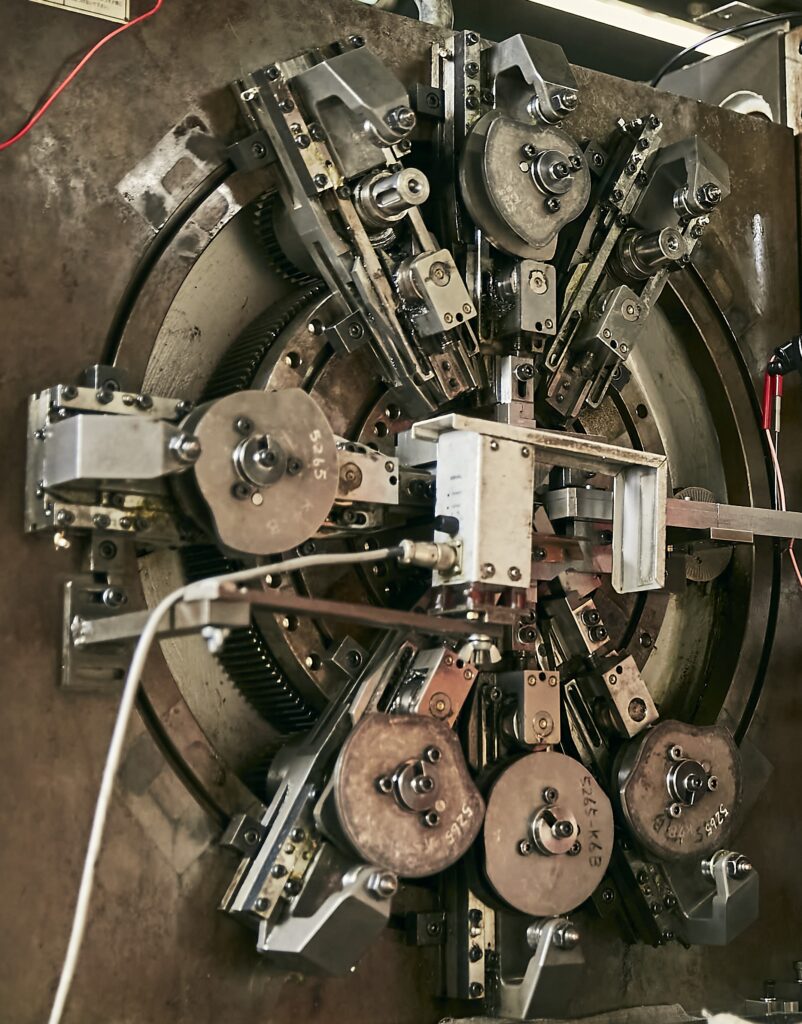
クイックファスナーをはじめ、板バネの製造工程は「曲げ加工」を組み合わせておこないます。曲げ加工とは、ブランクに圧力をかけてその材料を永久変形させる加工のことで、前回紹介したマルチフォーミング・マシンでおこなっています。
機械でスムーズに曲げ加工を行えるように、アームの動きや順番といった「曲げ工程」を考えた後に「曲げ越し量」を考えていきます。
曲げ越し量
「曲げ越し量」とは、図面で指定されている形より多めに曲げる量のことを指しています。
バネには、曲げ形状をつけても元に戻ろうとする「スプリングバック」と呼ばれる性質があったり、後処理工程などで製品の寸法が変化したりするなど、製品図通りの曲げツールなどを作っても想定した仕上がりの製品になりません。
クイックファスナーは、材質に「SUS材」と呼ばれるステンレスを使用されることが多いのですが、一般的にステンレスはスプリングバックが大きく、テンパ(熱処理)を行うと形状が開いていくことが多いことから、あらかじめこれらを考慮して完成品の形状に対して、より多く曲げる「曲げ越し量」を考えていくことが必要です。
曲げ越し量を計算した図面を作成後、その製品形状に合わした曲げツール、心金、コアホルダー、蹴り出しなどといった部品図を作成します。これらを経てレイアウト設計が終了になります。
カムタイミングの設定
レイアウト設計が終われば次にカムタイミングの設定です。
マルチフォーミング・マシン…カム式とNC機
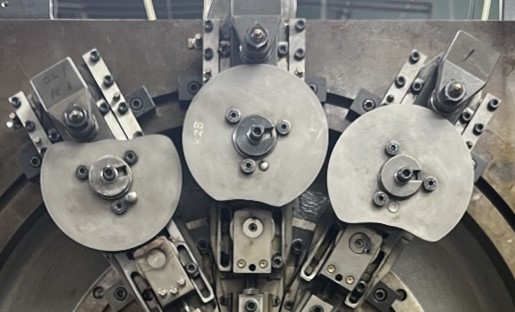
「カム」とは、カム(cam)は運動の方向を変える機械要素のことで、車のエンジンなどに使われています。カム式のマシンでは「押しカム・戻しカム」といった複数のカムを併用し、物理的なタイミングを決めて成形加工を行います。
光洋のクイックファスナーは基本カム式で加工を行っています。
NC機の「NC」は数値制御(Numerical Control)の意味で、プログラムで数値を入力することによって、タイミングを決めて成形加工を行うものになります。こちらは、後からも容易にタイミングを変更できることが特徴です。
まず、心金、コアホルダー、曲げツール、マニホールド、蹴り出しなど必要箇所の部品図を登録します。登録の際には、曲げツールがどれだけ上下に動くかストロークも入力していきます。
次にタイミングです。
この段階になると順番などは既に決まっているので、どのタイミングから上がり、どのタイミングで下がるか、1周360°の中で全体を見つつ安全な加工が出来るか確認を行いながら微調整していきます。
タイミングの調整が終わればカムの作図、製作という流れになります。
トラブルポイントの検討
部品図の全図面化が終われば最後にトラブルポイントの検討です。
レイアウト構成、部品図が出来た状態で材料の走行に障害は無いか、プレス内で異常が起こらないか、フォーミング内で心金や曲げツールに破損起因が無いかなど、安定した生産が行えるかを考えます。
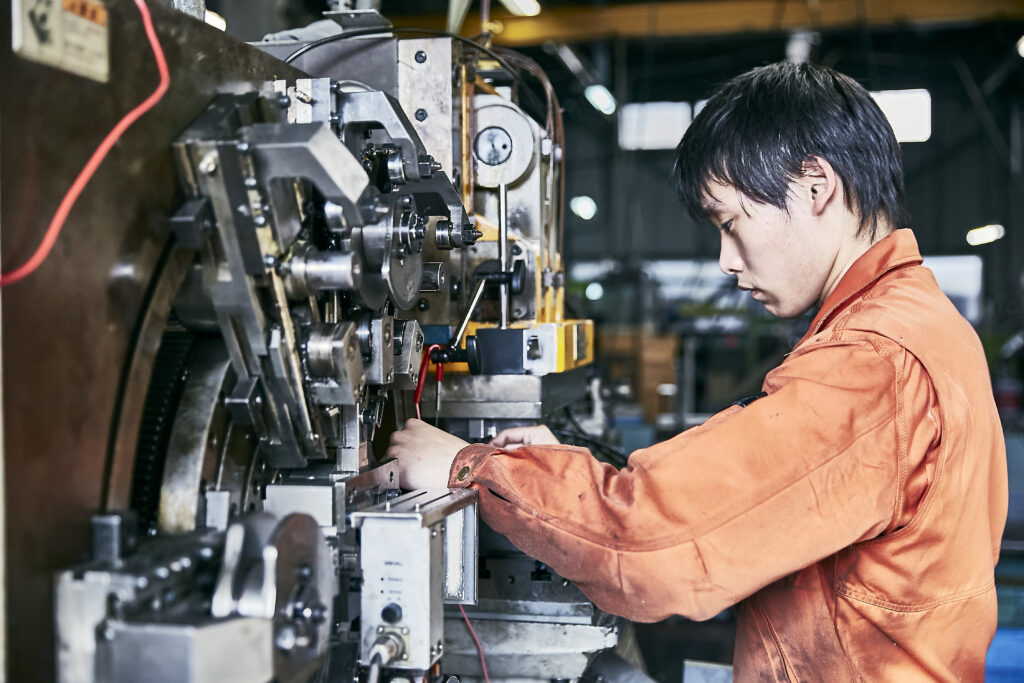
クイックファスナーのような板バネは、平面の金属板に曲げ加工をおこない、製品の形状にしていきますが、その工程の中で製品の「振り回し」が発生します。
振り回しとは、ブランク(材料)を曲げる際に、曲げた部分が動く範囲のことです。マルチフォーミング・マシンは加工範囲が決まっているので、生産を安定して行っていくためにも、製品を曲げる際に装置に接触する事が無いよう考慮する必要があります。
製品形状が左右対称であれば、ブランクの中心と加工原点が合うように考えれば、特に問題ありません。一方、左右対称でない場合は、振り回しの際に装置に接触する可能性はかなり高くなるため、ブランクの中心を加工原点とずらした設計にするなど、注意を払います。
製品形状が小さいパターンのトラブルポイント
小さい製品の場合、心金に対し曲げ加工をする製法では、心金のサイズが製品と比例して小さくなっていきます。心金が小さくなるという事は破損のリスクが上がり、安定な生産ができなくなる場合があります。
設計士はこの場合「心金の支えを追加する」「心金の形状を変え、少ない力で曲がるようにする」「生産のスピードを変え、反動を抑える」「心金を使用せず、ツールで形状を作る」など様々な選択肢の中から、いかに破損リスクを下げるか、最適な手法を常に模索しています。
このように、設計士は生産で起こりうるトラブルをある程度事前に把握しており、その中で起こりうるトラブルポイントを設計に織り込み、製造現場と情報を共有することで、生産の安定化を図っています。
関連ブログ
-
板ばねの「マルチフォーミング加工」に焦点を当て、詳しくご紹介します。...
-
身近な「ばね」を探してみよう!ファインディング・バネ~家編~
ばねは身の回りのいたるところに使われています。今回は家の中にあるばねを写真ととも... -
金型保全体制について
光洋の金型保全 金型保全とは、金型や金型加工用の機械の適時点検をして手...