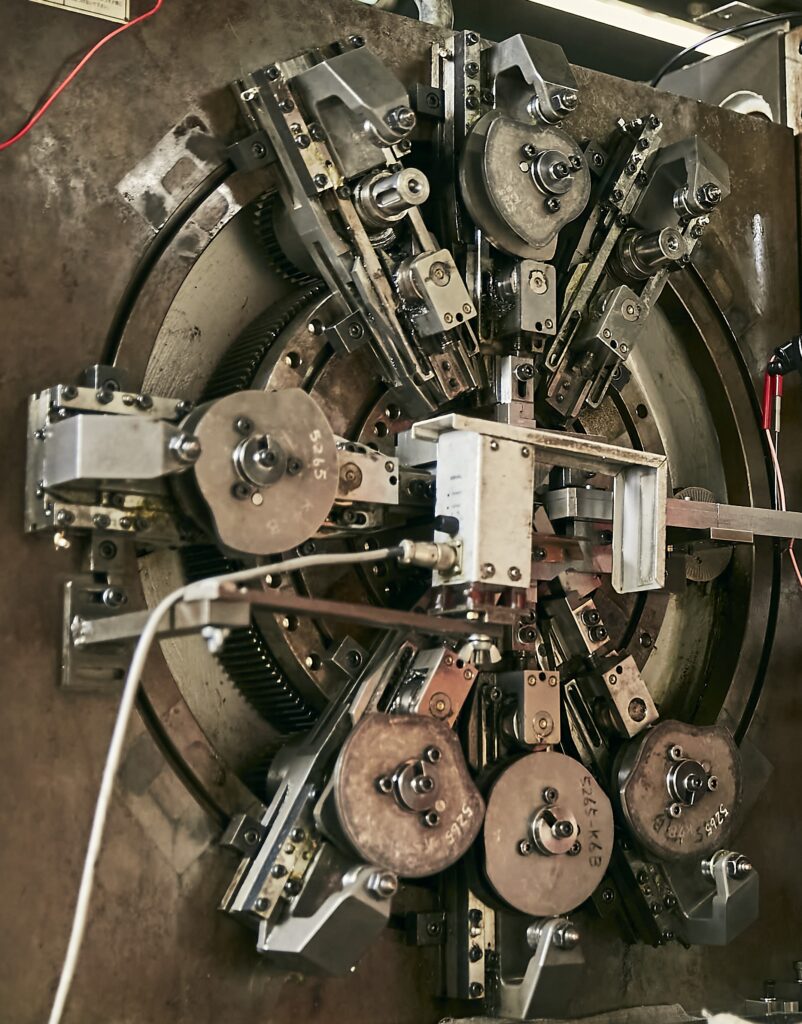
2023.06.12
会社情報昨今の情勢からどの会社も「経費削減」には力を入れていると思います。製造会社はもちろん、あらゆる企業にとってこのテーマは昔から続いている永遠のテーマとも言えるでしょう。
製造場面における経費削減の至上命題は「生産性向上」です。表題にある「品質ロス金額の低減」もそのひとつ。私たちは、製品を作る上で発生する問題を一つずつ潰していく事で色々なロスを減らし、生産効率の向上を実現していこうと取り組んでいます。
品質ロス金額とは?
「品質ロス金額」とは、不具合品の処置にかかった費用のことです。
光洋の不具合品は以下2つに分類されます。
①客先流出不良、不具合情報
製品をご使用していただいているお客様が不具合を発見され、光洋へ連絡があったもの。
(当面の処置を行った後に原因の究明と対策をおこないます)
②異常ロット
製品が出荷されるまでの間に不具合が発見されたもの。
(初工程で生産された製品は各工程で中間検査を行いながら、製造ロットごとに移動・処理されます)
何らかの原因により不具合品が発生したとしても、①は本来あってはならないもので、②の段階でいかに流出を止めるかが重要になります。致命的な不具合や不十分な対応は、お客様の信用を失いかねません。そのため、品質ロスの問題は迅速に解決する必要があります。
不具合の発生源を探る「4M」
4Mとは【方法(Method)材料(Material)、設備(Machine)、人(Man)】のことで、不具合が発生した際、これらを切り分けてどこに要因があるのかを探っていきます。そして、その要因にあった処置を取るようにしています。
・製品の不具合を防ぐ記録「Method」
光洋では主に線ばねと板ばねの2種類を生産していますが、板ばねの場合は方法(Method)を更に分けて、金型という分類も設けます。
板ばねの製造には、製品ごとに設計された金型を使用するのですが、これらが製品不具合の要因となるケースがあるからです。
製品の不具合や異常ロットが発見された場合は「不良処理表」や「異常ロット処置報告書」が発行され、発生した日時や現象・発生場所(工程)はもちろん、処置方法や損失費(廃棄重量)など細かく記録され『年度別不良処理ファイル』として保管されます。
このデータは年度別に蓄積されて、改善活動に活かされ、根本的に同じ不具合品を流出させない体制を取っています。
・納入品の細かな確認「Material」
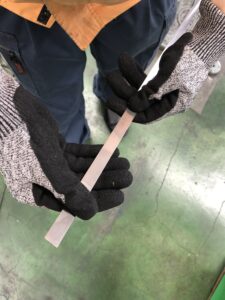
材料(Material)の例では、板ばね、線ばね、共に発生することがあるのですが、納入されたものに不具合があり、そのまま生産するには加工上、品質上に問題がある場合です。
これらを防ぐために、使用前に寸法や変形(線癖、キャンバー*など)の確認は勿論のこと、色味や微細キズなどの表面状態を注意深く観察します。
その際「どんな小さな気づきでも違和感が有れば上司へ報告・相談」を徹底しており、現場作業者から報告を受けた時には上司や品質保証部でも確認を行うことで、ムダの最小化に取り組んでいます。
*キャンバー(曲がり)…コイル状に切断された銅版が板幅方向に曲がること
・稼働を止めない日々の点検「Machine」
弊社の加工設備(Machine)は、その稼働年数や状態も様々です。そのため、日々の日常点検をはじめ、生産管理システムと連動させ一定の生産数ごとに行う定期保全など、常に稼働可能な状態が保持できるようメンテナンスに努めています。
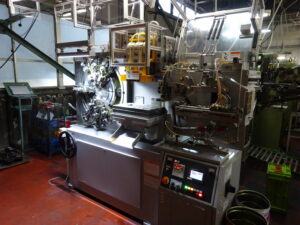
マルチフォーミング・マシン「PROFORMA RF-60」
しかし、中には製品の特性上負荷が高いものも存在し、予測より早いタイミングで不具合が発生してしまうこともあります。この際にも保全タイミングとなる生産数サイクルを短縮するなどの処置を実施し、以降の生産に影響のないように管理を徹底しています。
・作業手順を明確にして管理「Man」
そして最後に人(Man)です。新しいばねを量産する際には、製品ごとに作業手順・標準書を作成します。それらは「製造履歴ファイル」として整理され、製造現場に保管されており、次に製造する際、誰が行っても同様の手順で製品を作ることができ、品質が確保されるようになっています。
品質ロスを減らすための強い意志
光洋の不良件数や、それらにかかる費用は年々、着実に減ってきています。
しかし、不良の発生をゼロにするということは難しいものです。
だからこそ生産中の早期発見と、そして根本的に発生しない仕組みづくりをこれからも進めていき、品質ロス金額低減に努めていきます。
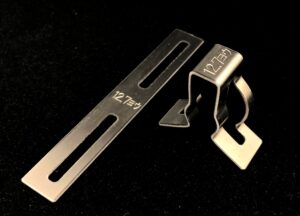
関連ブログ
-
板ばねの「マルチフォーミング加工」に焦点を当て、詳しくご紹介します。...
-
身近な「ばね」を探してみよう!ファインディング・バネ~家編~
ばねは身の回りのいたるところに使われています。今回は家の中にあるばねを写真ととも... -
金型保全体制について
光洋の金型保全 金型保全とは、金型や金型加工用の機械の適時点検をして手...